Accessible on cloud or deployed on private servers, Dolphin Service center seamlessly integrates with Dolphin ERP & Dolphin JobDor Mobile APP.
Dolphin Service Center is the ideal solution for repair centers and service center operations. Can be applied on a wide variety of Goods and Product types such as smartphones, televisions, home theater systems, Home Appliances, computers & laptops, medical equipment, wearable devices, smart appliances, marine equipment & even heavy equipment.
It has been designed for use in a Client Servicing Help Desk or a Call Center, for creating tickets (for example to register a complaint for technical defects). It can be applied in cases where repairs are covered by maintenance agreements (SLA,…) or even for ad-hoc repairs.
Dolphin Service Center makes it easy to manage repairs taking place at a workshop, in a repair center or even at the client’s premises, contributing to boost the company’s performance for efficient and on-time repairs, and to help ensure the best client satisfaction.

Preparation of quotations is done following an inspection of the defective Item or Equipment. It involves the cost of labor, material (parts & consumables) and some
outsourced costs.
Customer billing may be generated based on a submitted and approved quotation, or based on the Material spent, Timesheet of Labor & Technicians, and Direct Expenses carried out on the job.
The automatic billing generation considers the existence of warranties with respect to its terms, or to annual maintenance agreements (SLAs). These could cover labor fees, and/or spare parts depending on the cases.
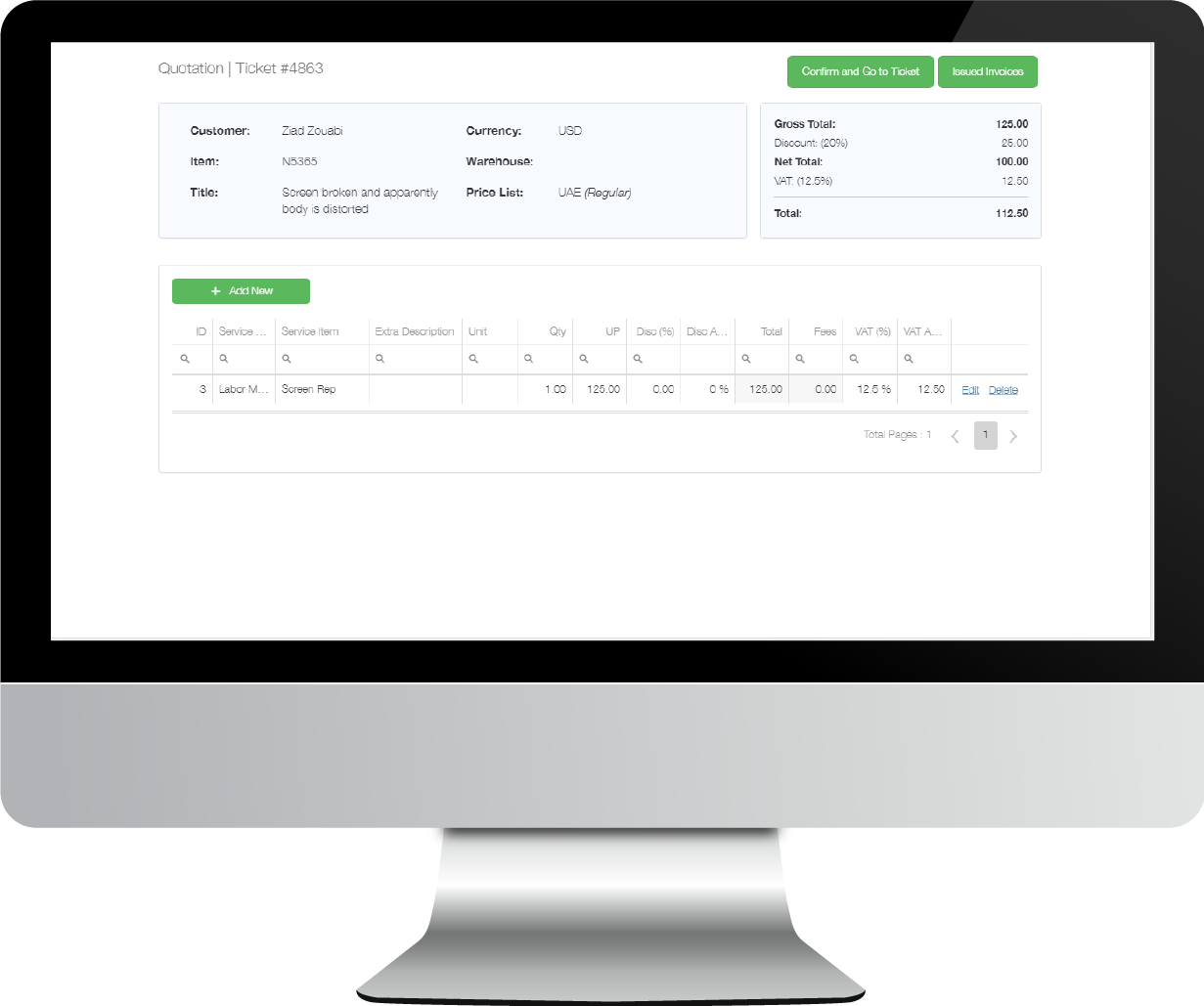
- Cost estimate of the repair (needs of spare parts and labor time)
- Client quotation
- Invoice may be generated based on a quotation, or, on the items & time spent
- If Item under manufacturer’s warranty, invoices may be generated to the manufacturer
- If Item under sub dealer’s warranty, invoices may be generated to the Sub dealer
- Shipment fees for courier delivery and VAT rates apply
Designed to help manage and enhance the efficiency of Workshops and use of spare parts. Repair orders can be created and problems diagnosed in order to produce a first estimate of the repairs to be done. During repairs execution, the module keeps track of the labor time spent and the spare parts used on the Ticket. A timesheet allows every employee working on a specific job to register their time. Monitoring a job in progress can be made easy based on an integrated workflow, and a series of managerial views, alerts & reports.
Tracking by serial numbers helps checking on warranty status based on international warranty coverage, company’s warranty, or, on an annual maintenance agreement (annual retainer or subscription).
A built-In CRM features an integrated Contact Management & Client Information System, Client History, Item’s track record of previous repairs and/or Maintenance Action performed, Direct Mail updates to clients, Statement of accounts & Balances, Visit reports…

- Friendly way for creating new tickets and Job cards
- Client Quotation & Billing (including Spare Parts and Labor)
- Dispatch tickets to the Technical department through a workflow
- Check on Warranty coverage
- Check on History of Repairs based on the item’s serial number
- KPIs on response time for the item repairs
- Items may be swapped (if covered by the warranty) or repaired
- Several analysis and dashboards on type of repairs,
- Job Revenue and Profitability Reports sent to head office and manufacturers on list of fixes and repairs (RMA)
- Repairs may be done at client premises, in store (walk in customer) or in a workshop (Item sent by courier)
- Inventory of parts with equivalent part numbers
- Repairs may be covered by a warranty, by a maintenance agreement or may be invoiced to clients on a case by case basis.
Many forms of warranties apply depending on the type of products and on the business model of the service center. These may be international, or granted by the dealer; they may include extended warranty from the retail store or based on some annual maintenance contracts. For certified service centers, the system applies RMAs and a back to back billing with the manufacturer or the distributor.

- Warranty can be defined in many types (labor, Parts or both, with Exclusions of some parts)
- Company’s Warranty coverage if sold by the company
- Manufacturer’s warranty (International warranty that applies in certified service centers)
- Annual Maintenance based on Service Level Agreements
- Extended Warranty when the product is sold by the retailer
The generation of Task Work Orders is based on the repair tickets or on preventive maintenance actions pre scheduled and already due. The Task Work Order contributes to monitoring of Actions (Tasks) assigned to various technicians, and scheduling them in time as per the resource’s scope of specialization.
Accessible from any web browser (Mac or PC) or from a “JobDor mobile application”, a listing allows the monitoring of the tasks assigned to technicians, highlighting client or problem type. Similarly, tasks are displayed in a calendar giving a better view on the work’s distribution between resources (displaying names of Technicians, dates & time, task description, and length/duration. Also available, is a friendly way to drag and drop tasks moving them between team members of the same group, or rescheduling them to another date or time.
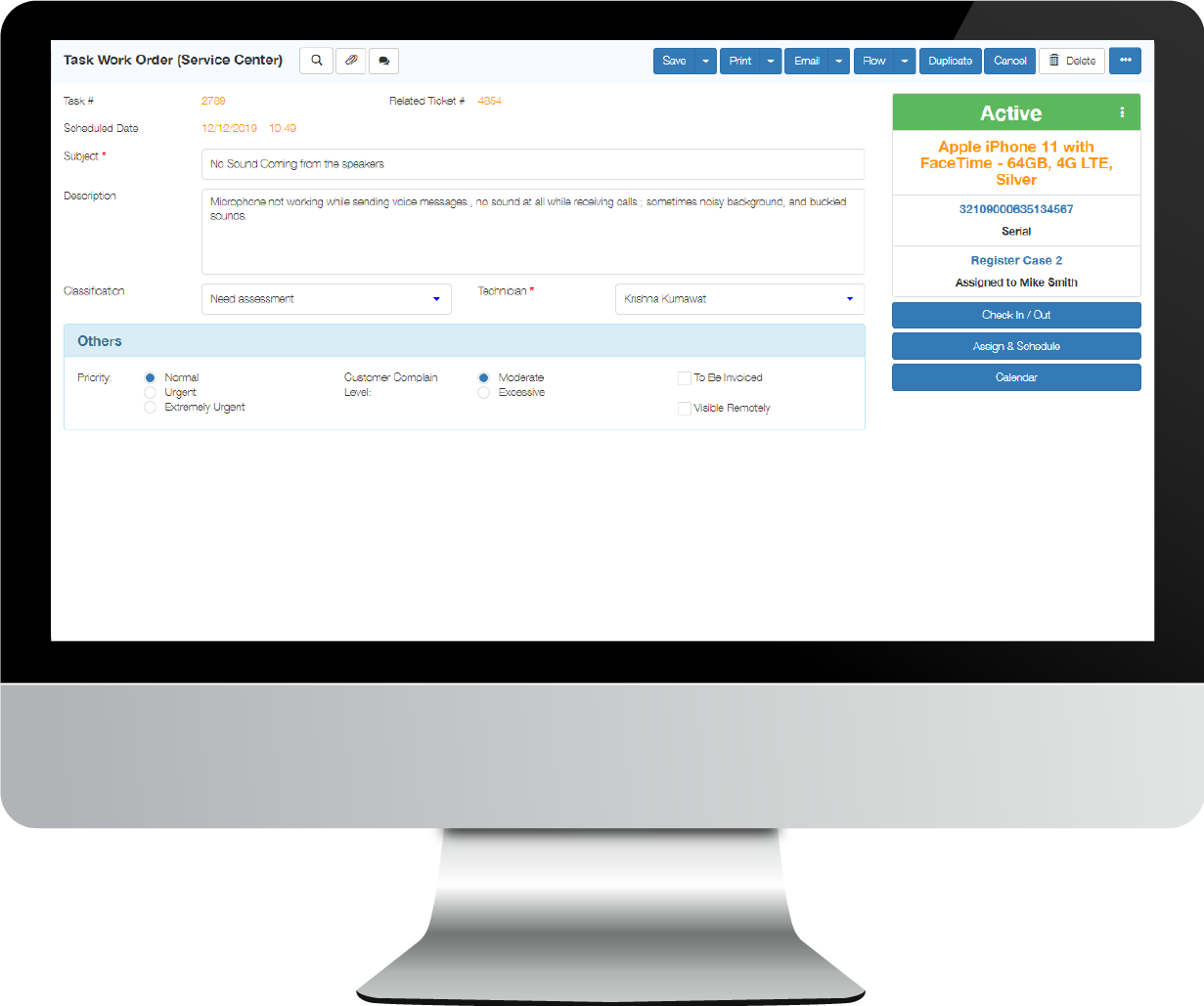
- In a workshop, possibility to assign tasks to technicians
- Tasks are scheduled with client’s appointments
- Technicians assignment of tasks are managed through a calendar with drag and drop
- Tasks are accessible through Dolphin JobDor Mobile APPs
- A Check IN and Check Out feature allows to measure the time spent on each task.
- KPIs measuring the duration between the time receiving a call and the time when completed.
- Tasks may be linked to a client, to a Ticket, or it may be stand alone.
- The system issues alerts when total time spent has exceeded the time estimate.
Dolphin includes a fully comprehensive Inventory Control System for spare parts tracking, Items reordering, transfers between stores and booking items. Dolphin also includes the concept of alternate part numbers through equivalent item codes or equivalent barcodes when supplied from various sources.
Prepared by the technical team, the material Pick list is a document that contains the list of parts to be issued from the stores on a ticket or on a project. Using the JobDor mobile app or simply using a web browser, the MPL is re routed to the store keeper for dispatching the goods. When quantities are not available the system fills a request for Purchase Orders.

- Integrated with Dolphin ERP
- The Material Pick List (MPL) allows selection of required parts for a repair
- Report on Item’s availability in stores or to be ordered
- Automatic Generation of Purchase Orders for missing quantities
- Multistore management
- Equivalent part numbers
- Generation of Material consumption transactions assigned to a Ticket or Job Card
- Itemize and track usage of parts, spare parts & consumables while maintenance is being performed.
Helps you stay on top of what needs to be done with planned preventive actions and repair maintenance alerts.
Dolphin Preventative Maintenance allows to schedule and track regular maintenance and inspections on Equipment, Items or Machineries. It helps preventing unexpected asset failure/breakdown and extend the life expectancy of the property or the equipment. Dolphin PPM Manages the regular maintenance to be conducted based on a specific frequency (once every quarter, or 2 times a year..). Accordingly, a planner will generate an annual calendar by creating tickets & tasks for each round of preventive inspection &/or action to be taken.
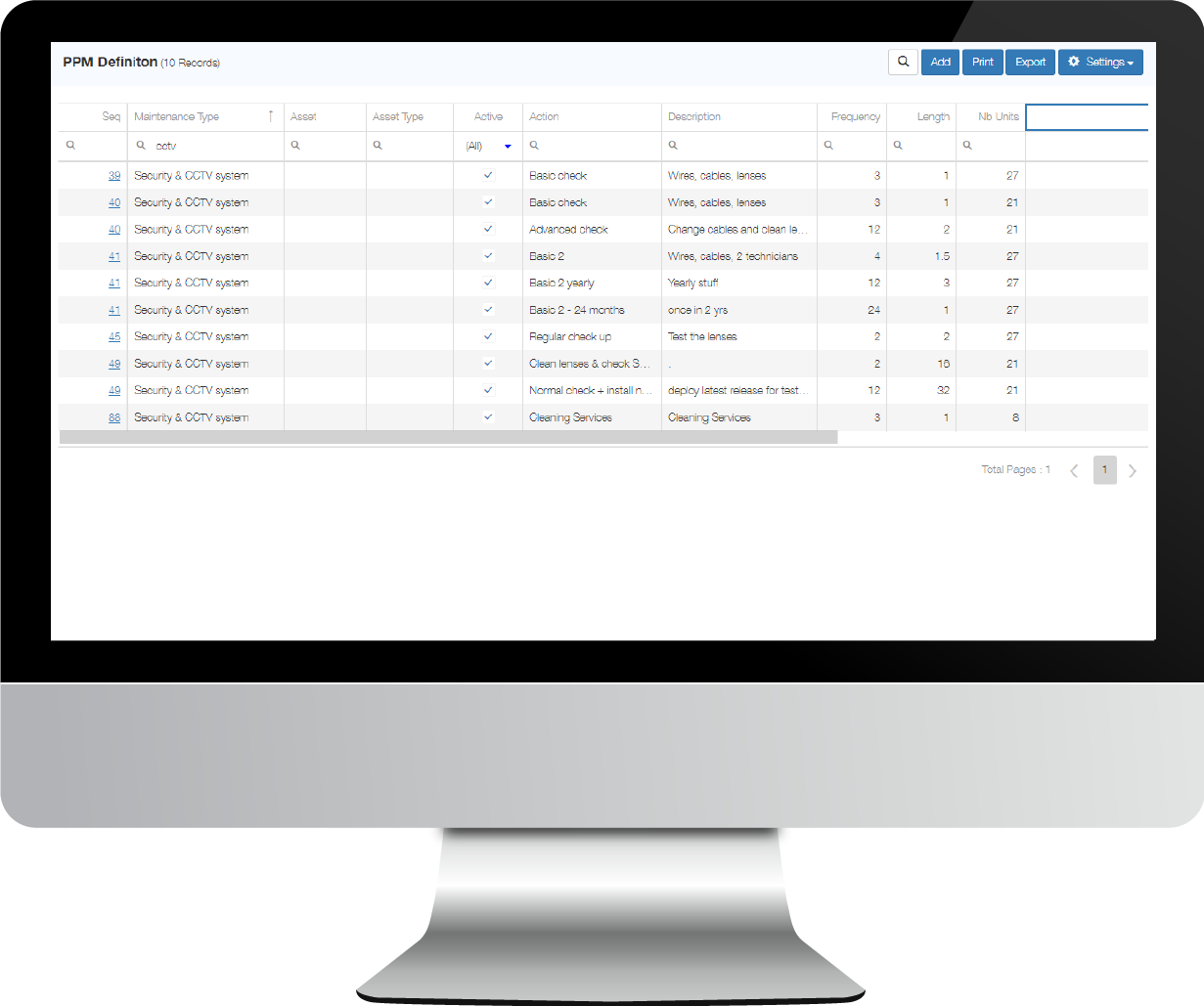
- Allows you to substantially reduce reactive maintenance keeping assets at the desired level of quality.
- Applies to Heavy equipment, Appliances, Healthcare or office equipment
- Scheduling for annual visits
- PPMs generate Task Work Orders along with Check lists on actions to be performed
- Planning for Preventive maintenance actions defined in cycles
- Dolphin Job Card & Task Work Order allows to plan, schedule and monitor the execution of all its PPM activities.
- PPMs based on Operating Hours, Odometer (or counter), or Time Duration in months
No proper servicing may be conducted without generating appropriate Inspection Checklists with each repair ticket to perform or preventive maintenance to undertake. For checking or for executions, the check list topics include as well recommendations & explanations to the technicians on the tasks to perform.
A long list of Actions may be defined with various possibilities of answers: From Very Good to Very Bad, or specific custom made reply options, or notes to be taken at the level of each action to take or to check.
Preset Checklist forms may be defined; these are automatically issued based on the type of ticket or inspection to be done.

- Applies with the tickets, the tasks or with preventive maintenance actions.
- May be filled through a mobile device (JobDOr Mobile App) or using a web browser.
- Multiple choice for answers
- To DO or to CHECK
- Preset forms including a set of topics categorized by problem type
- Attachment of pictures at the level of each topic of the Checklist
- Checklist results & KPIs are measured through Dolphin Analytics & Dashboard
- Alerts are given for the failed topics during inspection
Clients may fill repair tickets online, assign a coordinator (for follow ups), write notes & messages, view ticket status updates, review the history of all repairs done.
Upon closing a ticket, the system automatically sends an email with a set of questions to the customers, to help measure the level of client satisfaction. It establishes a score, rating again key performance targets aiming to improve the quality of the service in a company. That rating is displayed visually to help see its evolution over time, and gain a deeper understanding of whether servicing company is meeting its customer’s expectations or not.
- Once the repair is done, Dolphin sends a survey by mail to the clients for assessing their Satisfaction
- Clients may access the systems Online and review all repairs ever done in the past.
- Client portal gives access to the clients to post defects related to their equipment and monitor the repair status & delivery
- Tracking the outstanding tickets and reviewing their status
- Using the same portal, clients may check their financial balances including invoices and payments.
- Registration of users with a secured validation from back office
- Alerts are issued when no response to a ticket is registered within a specific time frame.



